Technology
GE Appliances doubles revenue through supply chain restructuring
Manufacturer relocates production to the USA – new inventory management revolutionizes processes.
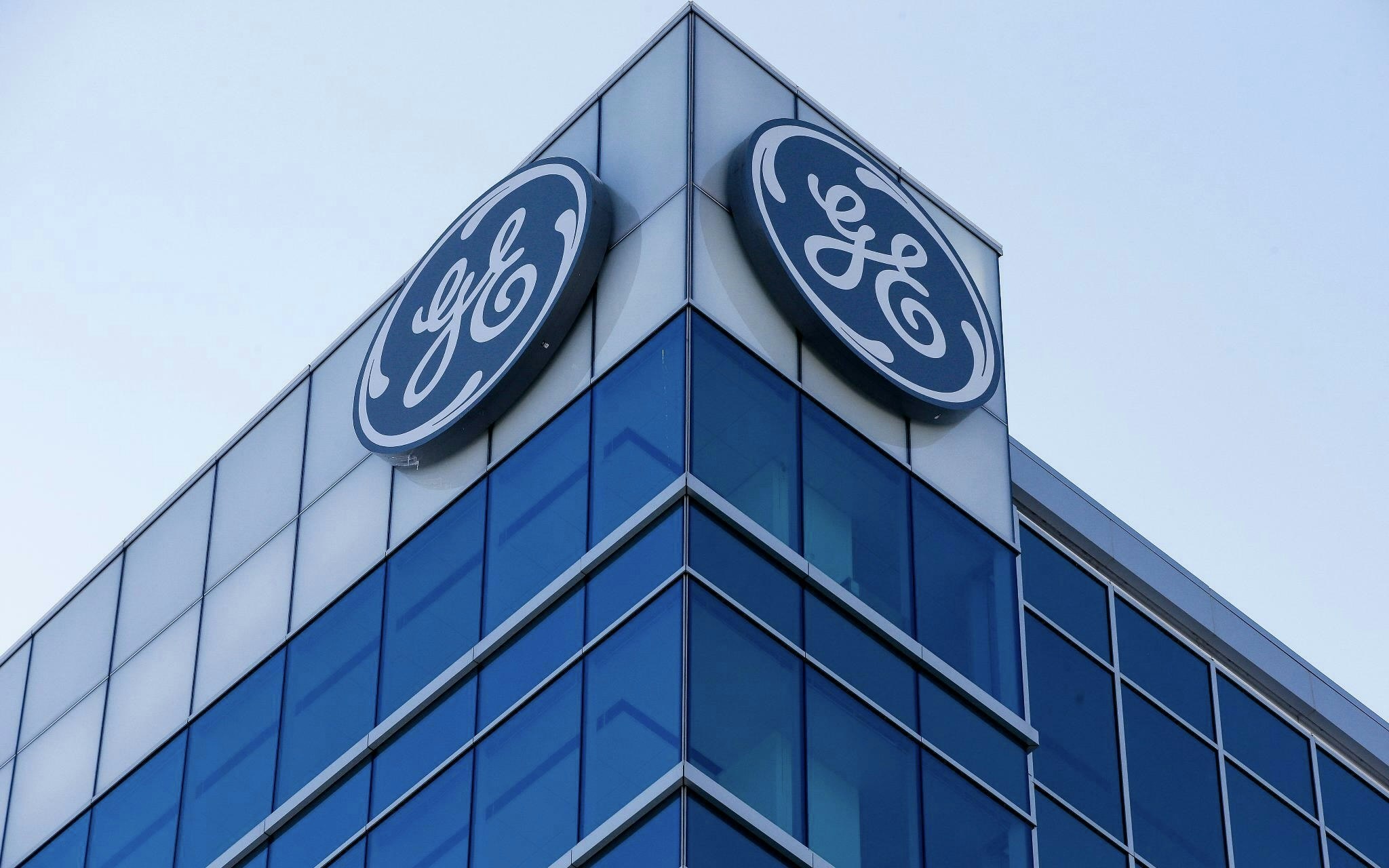
GE Appliances, one of the largest home appliance manufacturers in the USA, has achieved remarkable success through a comprehensive overhaul of its supply chain. The company, a subsidiary of the China-based Haier Smart Home, has doubled its sales since 2017. A $2 billion investment program has played a central role in this achievement.
The company based in Louisville, Kentucky, has expanded its production capacity, opened seven new distribution centers, and implemented digital tools to optimize operations from production to delivery. Marcia Brey, Vice President of Logistics at GE Appliances, emphasized that these changes were necessary to gain market share and strengthen the supply chain following product shortages during the pandemic.
The way we managed distribution not only required incremental improvements," said Brey. "We had to take a step back and ask ourselves: 'Are we really set up the way we should be?'
The restructuring began as early as 2017, years before the pandemic, to better align production and demand. During the pandemic, the company accelerated its efforts despite the challenges posed by product shortages due to the increased home improvement projects by consumers.
One of the biggest changes was the shift of part of the production from Asia to the USA. In the past seven years, GE Appliances has created 4,000 new jobs in its nine US plants. The relocation of production to the USA has reduced shipping costs and given the company more control over production.
If you have something in a container on a ship that is at sea for six weeks, it is difficult to adjust your orders and respond to demand fluctuations," said Rob Handfield, Professor of Supply Chain Management at North Carolina State University.
Another important step was changing the way GE Appliances measures its inventory. Previously, the company tracked "Weeks on Hand," which measures finished products relative to weekly sales figures. Now, it tracks the on-time and complete delivery of customer orders. This measure prioritizes existing orders, ensuring the company does not produce products that are not in demand.
To facilitate this change, GE Appliances has installed digital tools that allow the factories to view upcoming customer orders. The plants can then manage production schedules so that orders are completed on time but not too early. Storing bulky, fragile devices in a warehouse for a long time consumes space, increases storage costs, and heightens the risk of damage.
Today, I know that I am producing a unit because I have an order," said Brey. "In the past, I had no idea for whom I was producing it. I produced a lot to have a certain quantity in our network.
Through these measures, GE Appliances has improved its inventory turnover rate by about 50% since the pandemic. By having the right goods at the right time in the right place, the company was able to increase its market share.
The products are stored in distribution centers in the USA until the order is ready for shipment, to avoid stock in areas with no demand. GE Appliances also predicts the likelihood that customers are willing to receive the items at the forecasted time.
Retailers like Home Depot and Lowe’s usually require their orders to be on time, while property developers often grapple with material shortages and delays. These insights help GE Appliances' factories and distribution centers manage production and shipping schedules efficiently.
I want to produce the product as close as possible to the time the customer wants it," said Brey.